2021 – Made Smarter Case Study
Bloom-in-Box
Embracing technology to drive eco innovation
“Using technology is not about removing jobs but becoming more profitable and redeploying staff in other areas that benefit the business”
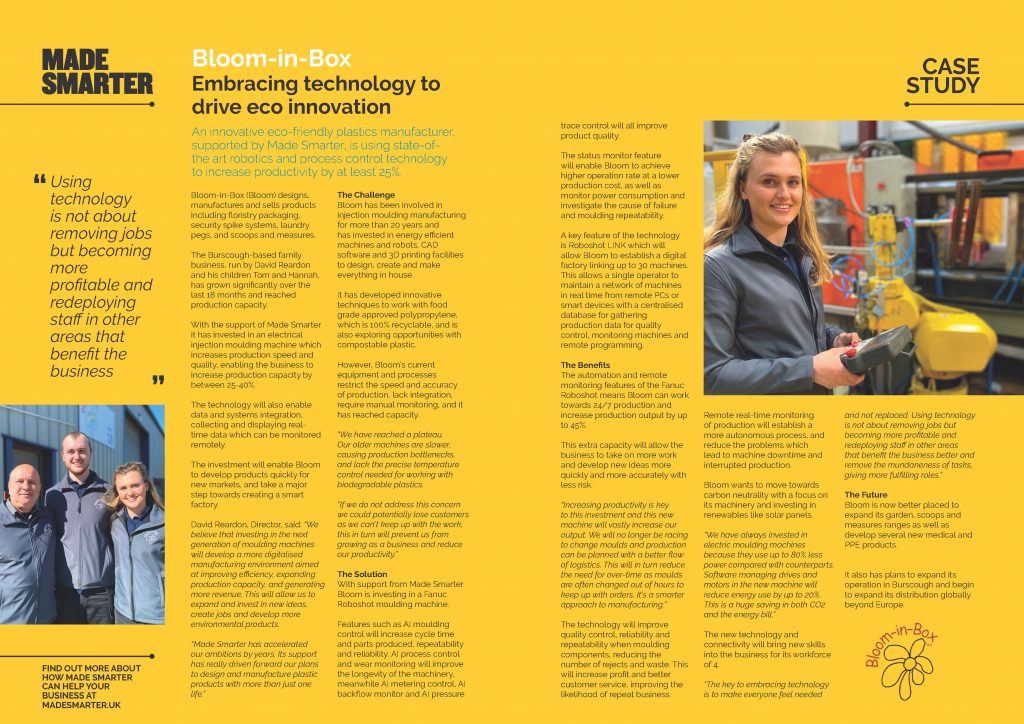
www.madesmarter.uk/resources/case-study-bloom-in-box/
Article Text
Bloom-in-Box (Bloom) designs, manufactures and sells products including floristry packaging, security spike systems, laundry pegs, and scoops and measures. The Burscough-based family business, run by David Reardon and his children Tom and Hannah, has grown significantly over the last 18 months and reached production capacity. With the support of Made Smarter it has invested in an electrical injection moulding machine which increases production speed and quality, enabling the business to increase production capacity by between 25-40%. The technology will also enable data and systems integration, collecting and displaying realtime data which can be monitored remotely. The investment will enable Bloom to develop products quickly for new markets, and take a major step towards creating a smart factory. David Reardon, Director, said: “We believe that investing in the next generation of moulding machines will develop a more digitalised manufacturing environment aimed at improving efficiency, expanding production capacity, and generating more revenue. This will allow us to expand and invest in new ideas, create jobs and develop more environmental products. “Made Smarter has accelerated our ambitions by years. Its support has really driven forward our plans to design and manufacture plastic products with more than just one life.”
The Challenge
Bloom has been involved in injection moulding manufacturing for more than 20 years and has invested in energy efficient machines and robots, CAD software and 3D printing facilities to design, create and make everything in house. It has developed innovative techniques to work with food grade approved polypropylene, which is 100% recyclable, and is also exploring opportunities with compostable plastic. However, Bloom’s current equipment and processes restrict the speed and accuracy of production, lack integration, require manual monitoring, and it has reached capacity. “We have reached a plateau. Our older machines are slower, causing production bottlenecks, and lack the precise temperature control needed for working with biodegradable plastics. “If we do not address this concern we could potentially lose customers as we can’t keep up with the work, this in turn will prevent us from growing as a business and reduce our productivity.”
The Solution
With support from Made Smarter Bloom is investing in a Fanuc Roboshot moulding machine. Features such as AI moulding control will increase cycle time and parts produced, repeatability and reliability. AI process control and wear monitoring will improve the longevity of the machinery, meanwhile AI metering control, AI backflow monitor and AI pressure CASE STUDY Using technology is not about removing jobs but becoming more profitable and redeploying staff in other areas that benefit the business “ “ trace control will all improve product quality. The status monitor feature will enable Bloom to achieve higher operation rate at a lower production cost, as well as monitor power consumption and investigate the cause of failure and moulding repeatability. A key feature of the technology is Roboshot LINK which will allow Bloom to establish a digital factory linking up to 30 machines. This allows a single operator to maintain a network of machines in real time from remote PCs or smart devices with a centralised database for gathering production data for quality control, monitoring machines and remote programming.
The Benefits
The automation and remote monitoring features of the Fanuc Roboshot means Bloom can work towards 24/7 production and increase production output by up to 45%. This extra capacity will allow the business to take on more work and develop new ideas more quickly and more accurately with less risk. “Increasing productivity is key to this investment and this new machine will vastly increase our output. We will no longer be racing to change moulds and production can be planned with a better flow of logistics. This will in turn reduce the need for over-time as moulds are often changed out of hours to keep up with orders. It’s a smarter approach to manufacturing.” The technology will improve quality control, reliability and repeatability when moulding components, reducing the number of rejects and waste. This will increase profit and better customer service, improving the likelihood of repeat business. Remote real-time monitoring of production will establish a more autonomous process, and reduce the problems which lead to machine downtime and interrupted production. Bloom wants to move towards carbon neutrality with a focus on its machinery and investing in renewables like solar panels. “We have always invested in electric moulding machines because they use up to 80% less power compared with counterparts. Software managing drives and motors in the new machine will reduce energy use by up to 20%. This is a huge saving in both CO2 and the energy bill.” The new technology and connectivity will bring new skills into the business for its workforce of 4. “The key to embracing technology is to make everyone feel needed and not replaced. Using technology is not about removing jobs but becoming more profitable and redeploying staff in other areas that benefit the business better and remove the mundaneness of tasks, giving more fulfilling roles.”
The Future
Bloom is now better placed to expand its garden, scoops and measures ranges as well as develop several new medical and PPE products. It also has plans to expand its operation in Burscough and begin to expand its distribution globally beyond Europe.